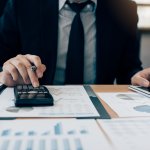
Carrying out
profitability-
calculations
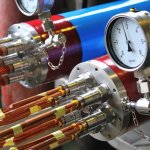
Measurement of volume flow, pressure
and heat losses
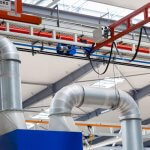
Technical pre-dimensioning and operating-
point calculation
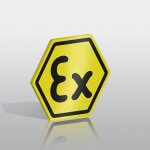
Preliminary design in dust and
gas explosion-
protection zones (ATEX)
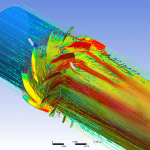
Flow simulation
including-
heat transfer (CFD)
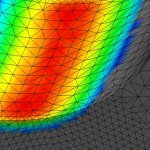